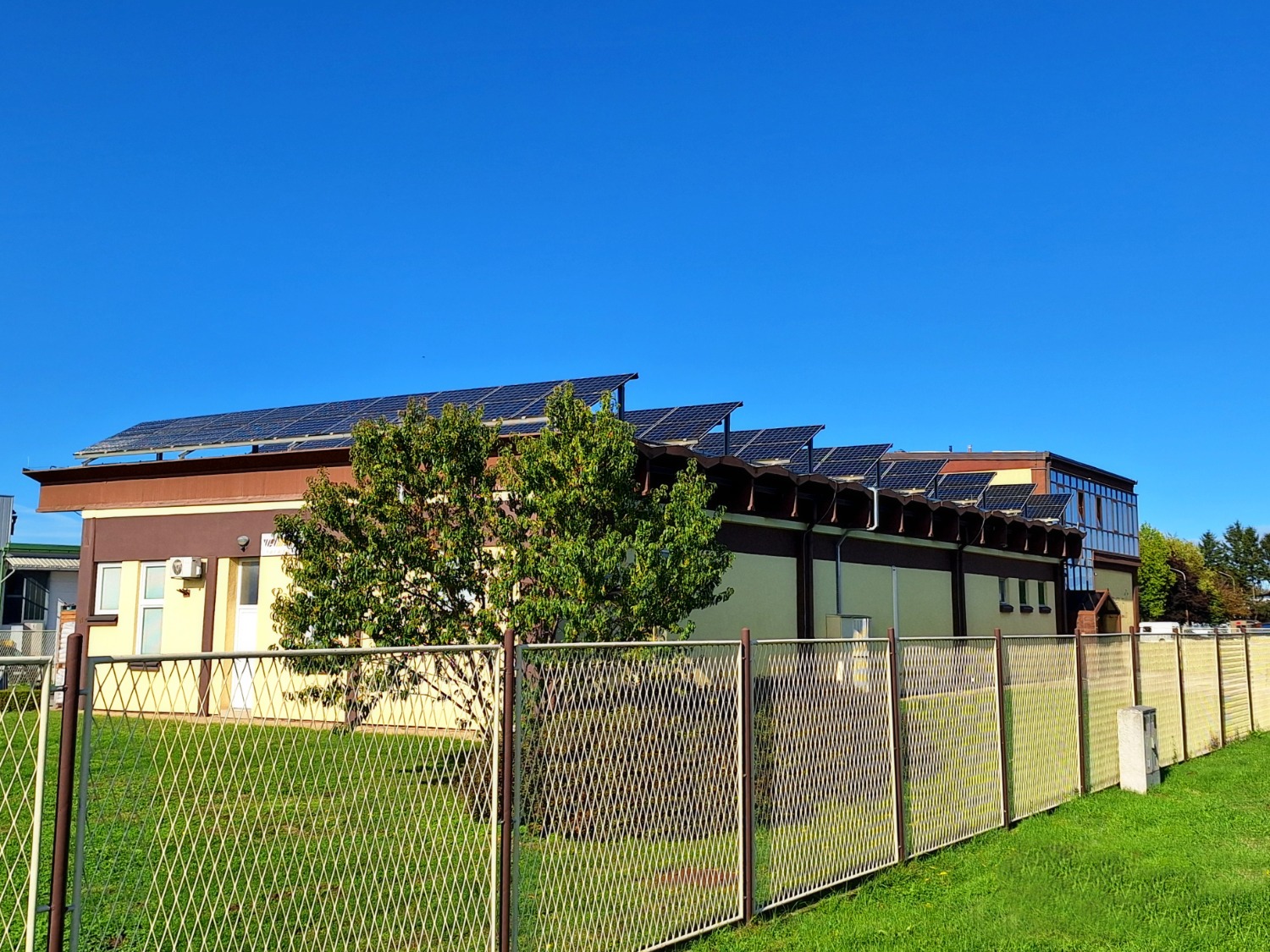
Conservation of bovine head skins and hides with sea salt
Find out the technological process in the conservation of bovine head skins to preserve them from spoilage and rotting. Also, find out how to prepare them for delivery in ship containers or trucks.
The technological process in the conservation of bovine head skins in our company begins after the raw skins/hides are transported from the supplier to the warehouse. The technological process consists of four main steps, which we describe below.
For more information about bovine head skins click here.
Delivery and salting of bovine head skins
The first step is delivering and unloading raw bovine skins in the warehouse’s cargo area. They are usually delivered by our truck and placed in waterproof box pallets. All bovine head skins have accompanied documentation.
The most important is the second step and that is preservation – salting the skins. They are salted with sea salt in two stages, where the amount of salt for salting is taken into account, and the whole process is carried out mechanically (drum-mixer or drum salting procesor) with the assistance of employees. This is a closed salting system in which any external influence is reduced to the lowest possible level.
Salting percentage for conservation of bovine head skins
In the first stage, raw bovine head skins are transferred from the box pallet to the drum mixer and mixed with sea salt. Optimally salted skin in this stage is approx. 15% of the weight of the skin. That is also standard for all parts of bovine/cowhides.
Salt has to be properly distributed over the entire surface of the skins with the help of a drum mixer. Skins can sometimes be salted with less salt, if the ambiance and storage temperatures allow it, but this increases the risk of spoilage and rotting, so less salting of skins is rarely practiced.
If they are salted with more salt, it will not have a better effect compared to normal salting, except in some unexpected circumstances.
We keep written records of salt consumption, so it is always possible to determine what percentage skins are salted.
After the drum-salting process, head skins are unloaded into the box pallets. They will remain in them for five to seven days. In this stage the salt penetrates the skin and drains the liquid, significantly slowing spoilage/rotting. Preservation of material is achieved.
Second salting, packing, and storage temperature
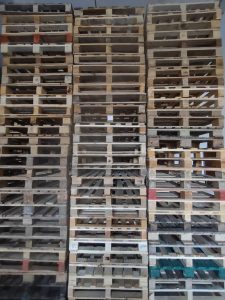
After five to seven days, it is time for stage two. Bovine head skins are salted again in a mixer. They are salted with an additional 10% of sea salt for complete conservation. The bovine skins and salt are put back into the mixer the same way, and the parameters from the first stage for turning the mixer are repeated.
After the completion of the salting process, skins are unloaded onto pallets into plastic bags where they will remain until the time of shipment (usually two to four weeks).
At the same time, it is good to monitor the temperature of the warehouse. The optimal temperature range for storage is from +4ºC to +18ºC. If the temperature rises above +18 degrees, we activate air conditioning to control temperature in the optimal range.
If it is impossible to control the temperature rise of temperature, it is necessary to frequently monitor the skins with more organoleptic examinations. Usually, skins need to be salted again to reduce the risk of spoilage.
The practice from the past, when we didn’t have a cooling system, showed that in the hottest months, when the temperature in the warehouse reached 30ºC, it was necessary to salt the skins with more salt. However, even then the skins did not have any serious signs of deterioration and rotting. Temperature below +4ºC generally has a positive effect on protecting them from spoilage.
Loading and shipment of conservated bovine head skins
The third step includes packing, palletizing and weighing of conserved bovine head skins before loading. They are packed in waterproof plastic bags so that during transportation there is no leakage of residual liquid.
Loaded container before it is closed and sealed for shipment.
Salted skins are sealed from all sides in waterproof bags, so leakage is reduced to a minimum to none. Now they are ready for weighing and shipment.
Normally, approx. 1100 kg of skins are stacked on one pallet.
The last fourth step in the technological process is the shipment (loading) of salted skins. Palletized skins are loaded under supervision by a forklift in a shipping container or tow truck along with documents that accompany the skins further along its journey. Short videos of that procedure you can see on our short videos on our Youtube channel and Instagram.
Clean wet-salted hides/skins warehouse
Another important step for business that is indirectly related to the technological process. It is maintaining hygiene in all working areas. Space sanitation is carried out regularly or extraordinary if needed. At the end of working hours, employees wash the floors and walls with water as well as other surfaces and work equipment. Periodically, more detailed cleaning is carried out, which includes the use of disinfectants.
The goal is to keep the work environment clean and as dry as possible. That greatly reduces the possibility of the development of bacteria.